Contact us for the latest range of professional Stick welders and consumables, or drop into our showroom at 500 Boundary St Toowoomba.
Single Phase Stick
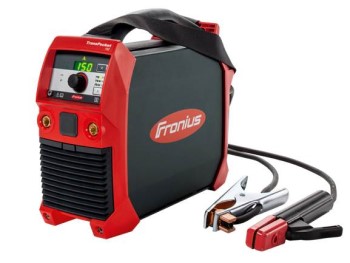
Fronius Transpocket 150 & 180
The TransPocket is available in power categories 150 to 480 A. In addition to the almost indestructible housing and cutting-edge technology, the TransPocket also has numerous functions that simplify work for the user: HotStart, SoftStart and anti-stick provide support at the start of and during the welding process.
The new generation of TransPocket 150/180 devices brings a high degree of flexibility. The integrated PFC (Power Factor Correction) technology supports the use of extremely long mains leads of up to 100 m in length. The operating concept has also become even more intuitive. A 7-segment display makes it possible to quickly read off the parameters that have been configured. In addition, the display is slightly set back and therefore well protected against damage. Easily comprehensible setup settings are a tremendous help in simplifying operation.
Kemppi Miniarc 150
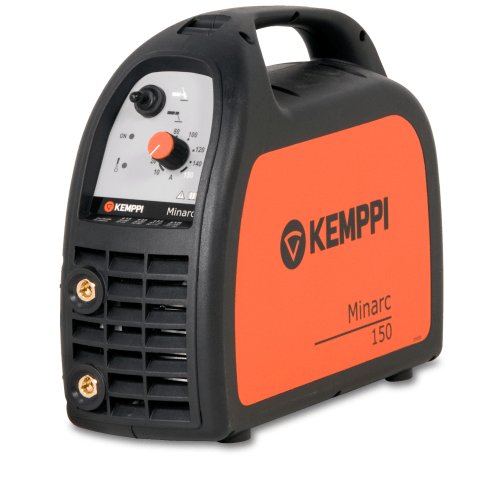
Minarc 150 is a 1-phase, 140 A DC MMA welding power source. This little powerhouse comes with everything you need to start welding. It has a durable casing and it is easy to carry with its shoulder strap. The Minarc 150 is also available with a VRD function.
Kemppi Minarc Evo 180
Minarc Evo 180 is the latest MMA model from the popular Minarc Evo family. It has all the great qualities of its predecessor, and then some. Upgraded, improved, and more powerful, it serves the agile welder better than ever with greater welding capacity. The delivery package includes both MMA welding lead and earth return lead and clamp. Every element of the Minarc Evo 180 is designed to meet the needs of professional welders on the move. Where size, weight, and welding quality are concerned, there is no equal.
BENEFITS
- Can be powered from the mains or generator power supply, even via extra long supply cables, thus ideal for on-site use.
- Easy to carry, so you can carry everything you need in one journey.
- Excellent arc stability in all welding positions and for a wide range of electrode types up to 4 mm electrodes, with large voltage reserves and automatic arc force control
- The capability to use with mains or portable power generators ensures that you always have power supply options
- Built for the welder on the move. The power source is housed in an impact resistant plastic casing
- Safe to use in damp or humid welding environments thanks to reduced Open Circuit Voltage (90 volts or lower)
- Save time by welding for longer, due to the reduced need for machine cooling breaks
- Reliable arc ignition reduces wasted time and increases welding quality
- A single machine covers a wide range of welding applications
- Easy to transport and carry onsite with a fast one man setup
Weldtronic Titan 141iSTV
- IGBT Inverter Technology
- Precise LIFT TIG Technology
- Digital LCD Display
- Excellent Arc Stability
- MMA/TIG Lift Start Switch
- Lightweight & Portable
- Self Adaptive Arc Force
- Fan Cooled
- Automatic Hot Start
- Simple to Operate
- Build in Voltage Reduction Device
- Infinite Amperage Controls
Bossweld Phoenix Electrode Drying Oven
The Phoenix drying ovens have been designed to maintain your low hydrogen electrodes at the best possible temperature during use, having excellent insulation properties which result in lower heat loss during heating and an adjustable temperature control so you can maintain optimum electrode conditioning. The construction and design of the Pheonix range of electrode ovens has taken into consideration the harsh environment which they are used, which will give the operators reliability when it counts.
Features
- Solid construction
- Adjustable temperature control
- Removable primary lead for safe storage
- Applications
- Electrode storage
- Electrode drying
- Improves electrode lifespan
Stick Welding
Stick Welding, also known as Shielded Metal Arc Welding (SMAW) or Covered Electrode, the most widely used of the various arc welding processes, utilizes a fixed length electrode and an electric power source to join a variety of different metals. The core of the covered electrode consists of a solid metal rod that is surrounded by a covering of mineral compounds and metal powders mixed with a binding agent to help them adhere to the surface of the electrode. The core rod conducts electric current to the arc and provides filler metal for the joint. The sizes and types of electrodes for Stick Welding define the arc voltage requirements (within the overall range of 16 to 40 volts) and the amperage requirements (within the overall range of 20 to 550 amp). The current may be either alternating or direct depending on the electrode used, but the power source must be able to control the level of current within a reasonable range to respond to the complex variables of the welding process itself.
The primary functions of the electrode covering are to provide arc stability and to shield molten metal from the atmosphere with gases created as the coating decomposes from the heat of the arc. This shielding controls the mechanical properties, chemical composition, and metallurgical structure of the weld metal, as well as the arc characteristics of the electrode. The composition of the electrode covering varies according to the type of electrode.
Why use Stick Welding?
Stick Welding is an extremely versatile process with respect to location and environment of the operation. Welding can be done inside, outside, on a production line, a ship, a bridge, an oil refinery, a cross country pipeline, or similar types of locations. Gas and water hoses are not needed, and welding cables extend significantly beyond the power source. In remote areas, gasoline or diesel-powered units can be used.
Equipment is relatively simple, inexpensive and portable.
Auxiliary gas shielding or granular flux are not required.
The process is less sensitive to wind and draft than gas-shielded arc welding processes.
It can be used in areas where access is limited.
The process is suitable for most of the commonly used metals and alloys.
Limitations
Operator duty cycles are low compared with semi-automatic and automatic processes; this makes the cost per pound of deposited weld metal high with Stick Welding.
Deposition rates are generally lower than for other welding processes.
The process is considered to be manual as it is not easily mechanized.
Stick Welding is not suitable for reactive metals such as titanium, zirconium, tantalum, and columbium because the shielding does not prevent oxygen contamination of the weld.